
At the end of the 1970´s asbestos was prohibited as an ingredient in the formulation of friction materials. Asbestos was not only very functional in improving the performance characteristics of the materials e.g. wear and friction, but it also assisted in absorbing noise and vibrations generated in parts of the braking system.
Since the prohibition of asbestos and its replacement in friction materials by other fibrous materials and metals, brake noise problems have increased to such an extent that studies show that it has become a major source of irritation to the vehicle driver. Solving of noise related problems is now of paramount importance to the vehicle manufacturers.
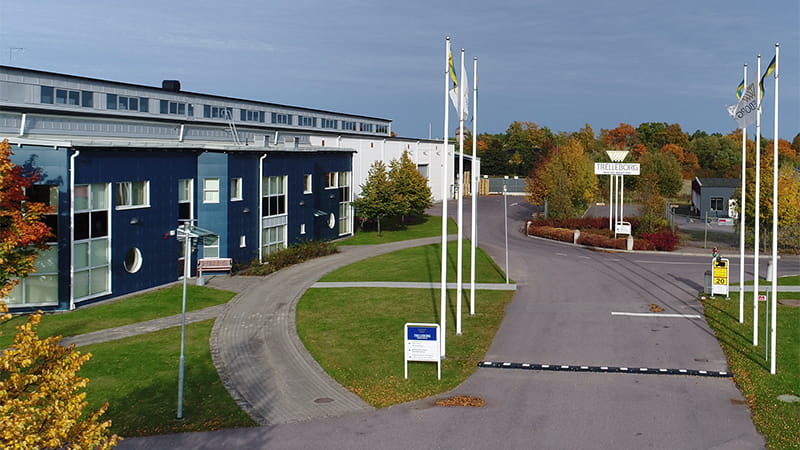
The company develops and manufactures noise damping shims, which when applied to the piston or finger side of a disc brake pad back plate provides an insulation. This barrier between the pad and the rest of the brake caliper absorbs vibrations and dampens any noise generated during vehicle braking. The shims are manufactured by the lamination of numerous combinations of rubber, steel, stainless steel, fiber glass and different adhesives.
The materials have unique characteristics, where the damping and isolating capacity of the rubber and adhesives is combined with the endurance of the metals against mechanical, thermal and chemical stress. A key feature of these shim materials is that, despite their complexity, they are thin, being around 0.6 to 1.2 mm.
The story of “Rubore” going from our founders kitchen to being the successful company it is today proves that with ingenuity, hard work, discipline and most of all conviction anything is possible.
Trelleborg Sealing Solutions Kalmar is today one of the worlds biggest shim producers, with their products installed in car and commercial vehicle brake systems around the Globe. The development of brake noise damping products has been very positive since
1988, with significant annual increases in turnover